Steam monitoring pays off in less than two years
ArcelorMittal Zenica reduces energy costs systematically
From manual calculation to automated measurement: turnkey steam monitoring solution enables the systematic reduction of energy costs.
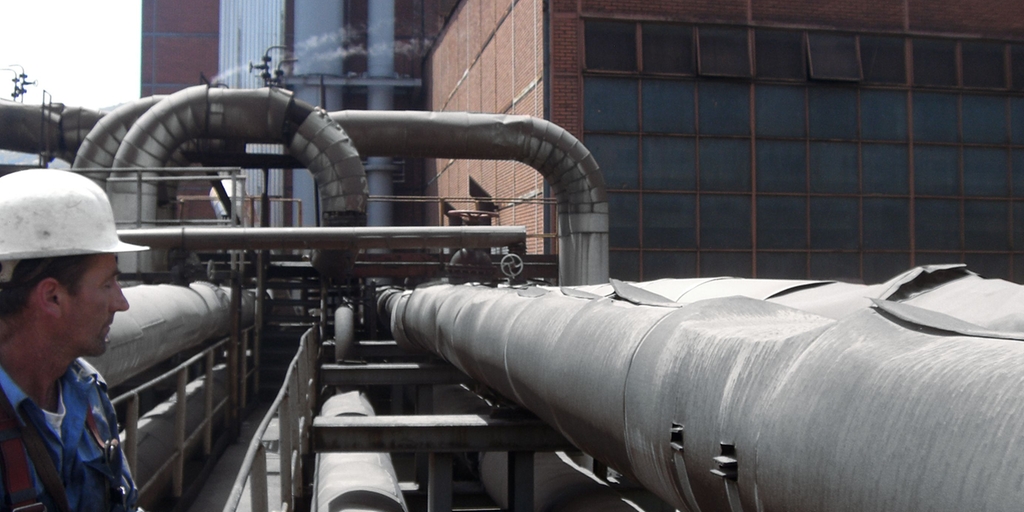
Identifying losses in transport is one of the main challenges for the Energy Plant Department that is responsible for the generation of steam used within the process and for heating purposes.
The results
Accurate, consolidated data on steam output, transport and consumption
Controlled steam consumption via precise metering of each consumer
Measured transport efficiency and allocated losses in the steam pipe network
Customized reports for management review
The challenge
Although steam consumption is very important to the profitability of the company, consumption by the different internal customers was only calculated according to empirical standards. As prerequisite for any efficiency gain actions, the Energy Plant Department needed to:
Monitor steam production and consumption in real time
Have meaningful data centrally available
Our solution
We integrated a turnkey steam monitoring solution into the company’s existing energy monitoring system. The solution includes:
Instrumentation and energy application managers
Data acquisition and visualization
Mechanical installation
Furthermore we also performed all the associated services that were required.
Solution components
Instrumentation: 39 steam measurement systems (Prowirl 72F vortex flowmeter + TR15 temperature sensor + Cerabar PMP51 pressure transmitter with syphon and shut-off valves)
Energy application managers: EngyCal RS33 including cabinets, cables and required system components
Data acquisition and visualization: P View software, OPC server and workstation PC Mechanical installation: flanges and reducer pipe works, insulation